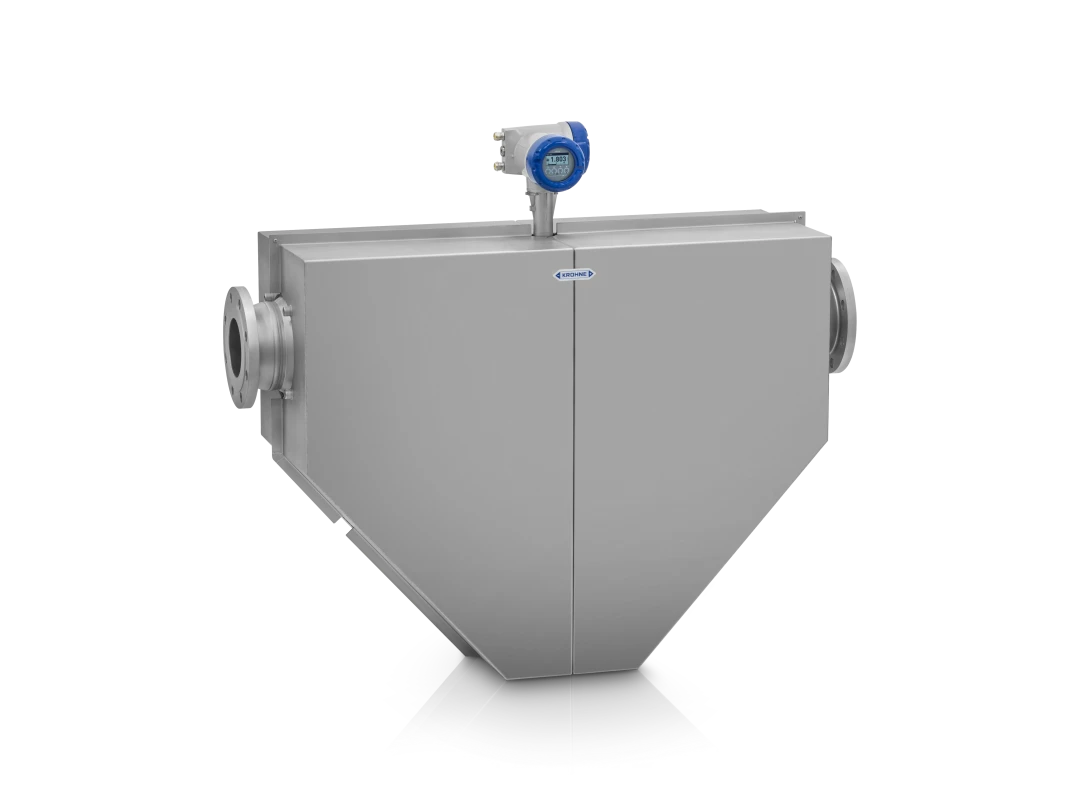
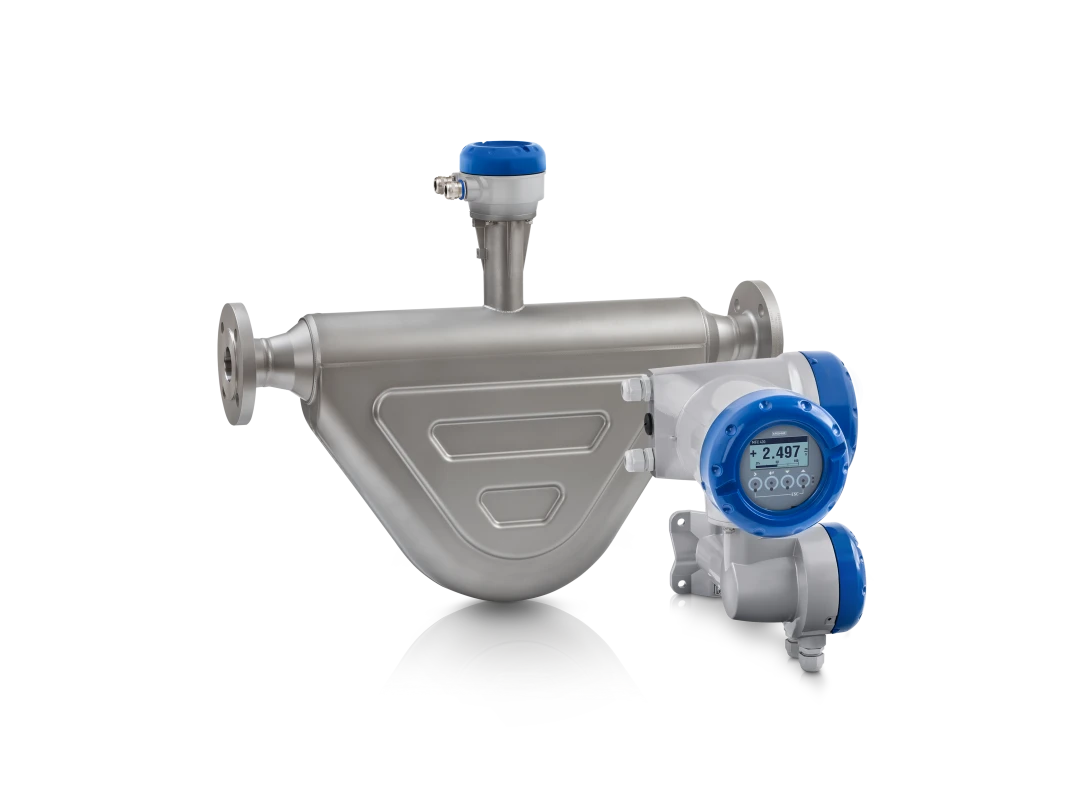
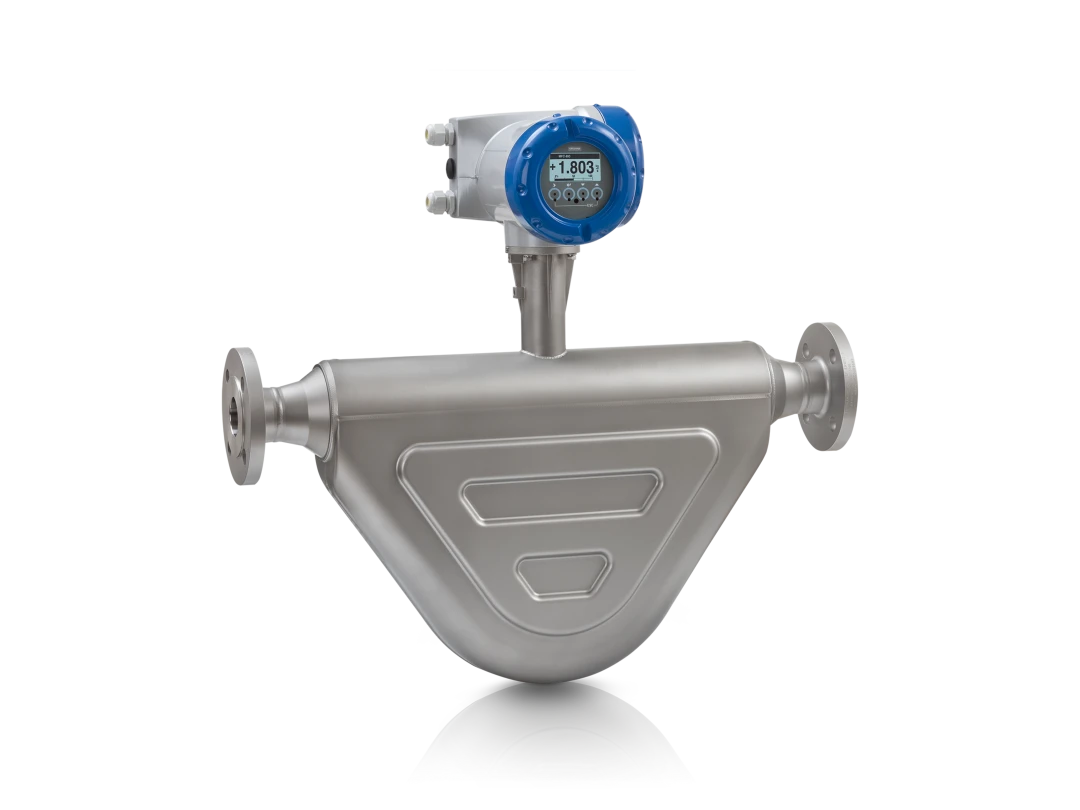
Mass flow measurement is crucial in many industries, ensuring precision in recipe formulations, material balance calculations, billing, and custody transfer operations. Given the importance of these applications, reliability and accuracy are essential when detecting mass flow. Coriolis mass flow meters have become the preferred choice for achieving high levels of precision and dependability.
The Evolution of Mass Flow Measurement
In the past, industries relied on volumetric flow meters paired with densitometers to estimate mass flow. These devices used measurements based on pressure, temperature, and density relationships. However, the lack of precise data often resulted in inaccurate measurements. Early attempts at mass flow measurement involved the use of angular momentum, where motor-driven impellers introduced complex and costly maintenance procedures.
The development of the Coriolis mass flow meter in the 1970s changed the landscape of flow measurement. This technology, based on the Coriolis effect, offers unmatched accuracy and is now widely used in various industrial applications.
Understanding the Coriolis Principle
The Coriolis effect was first identified by the French engineer G.G. Coriolis. He observed that objects moving on Earth’s surface tend to veer to the right in the Northern Hemisphere and to the left in the Southern Hemisphere due to Earth’s rotation. This phenomenon also influences ocean tides and weather patterns.
When applied to fluid flow, the Coriolis effect creates a deflecting force as the fluid passes through a rotating pipe. This force is directly related to the fluid’s mass flow rate. By measuring the force generated, Coriolis mass flow meters can determine the precise mass of the fluid.
How a Coriolis Flow Meter Works
Coriolis mass flow meters operate by vibrating a tube through which the fluid passes. As the fluid flows, Coriolis acceleration causes a twisting force in the tube, creating a measurable phase shift. This twisting force is proportional to the mass flow rate of the fluid, allowing the meter to calculate mass flow accurately. These meters can measure flow in both forward and reverse directions.
Typically, the vibrating tube is anchored at two points, similar to a spring-mass system. The vibration occurs at the resonant frequency, which is influenced by the fluid’s mass. Various tube designs, such as U-shaped or straight tubes, allow for flexibility in installation. Some models can even self-drain when mounted vertically.
Advancements in Coriolis Meter Design
First-generation Coriolis meters used single curved tubes. However, these faced challenges such as sensitivity to external vibrations and failure in corrosive environments. Modern designs use thicker walls, improved tube shapes, and heavy-duty materials to enhance durability and reduce interference. Recent innovations include dual-tube designs that improve performance by minimizing external vibrations.
Advantages and Limitations
Coriolis mass flow meters offer exceptional accuracy, often within 0.1% to 2% of the mass flow rate. However, certain factors, such as air pockets or gas in the fluid, can affect their accuracy. Additionally, temperature changes are continuously compensated for using built-in temperature sensors.
While Coriolis meters excel in measuring mass flow, density, and temperature, they may not be cost-effective for simple flow measurement applications where volumetric flow meters suffice.
Applications of Coriolis Mass Flow Meters
The versatility of Coriolis flow meters makes them valuable in a wide range of industries, from food and beverage to petrochemicals. These meters are ideal for measuring various fluids, including corrosive substances, making them an excellent choice for industries requiring precise mass, density, and viscosity measurements.
Applications include:
- Custody transfer in oil and gas operations
- Dosing and blending in food production
- Monitoring chemical processes in pharmaceuticals
- Ensuring accurate billing in utilities
Sizing and Pressure Considerations
Coriolis mass flow meters offer wide rangeability, from 30:1 to as high as 200:1, allowing for flexible sizing. Downsizing can be beneficial in cases where the pipe size is too large, provided the fluid is clean and has low viscosity. However, these meters typically experience higher pressure drops compared to volumetric flow meters due to their reduced tube diameter and circuitous flow path.
Interferences and Calibration
While Coriolis meters are highly accurate, they are sensitive to the presence of gas or air bubbles in the liquid, which can cause measurement inaccuracies. Regular calibration is crucial to maintaining their precision. Temperature fluctuations are accounted for with inbuilt sensors, which continuously adjust for any changes that could affect the readings.
Conclusion: The Future of Flow Measurement
The Coriolis mass flow meter remains the gold standard for accurate mass flow measurement in industries worldwide. Its ability to provide precise readings of mass flow, density, and temperature in a single device makes it an indispensable tool for critical industrial applications. As innovations continue, Coriolis meters will play an even more prominent role in optimizing fluid measurement processes.